Within this group project, we designed a Mars habitat, addressing the unique challenges of building on an isolated, foreign planet. These challenges ranged from atmospheric and surface conditions to varying pressure, radiation, and seismic activity levels. The project was developed with the intent of being produced and assembled with rovers prior to human arrival. Fragments, the solution for non-direct human intervention, are to be printed using Martian soil-based concrete and assembled using construction/assembly rovers. Grab holes were strategically placed based on the position of assembly and the rover's limitations. As a proof of concept, our assemblable fragments were carved out using a robotic arm programmed via Grasshopper
PLEASE NOTE: This was a group project; My specific contributions included conducting Mars-related research, site identification and analysis, design development, structural development, construction methodologies, digital modeling in Grasshopper within Rhino, and programming the robotic arm for fabrication
The design development of this project consisted of extracting Voronoi shapes from cubes to form the building blocks of the habitat. Voronoi shapes were chosen with careful consideration of the resources and construction on Mars allocated by the capabilities of the rover
Initially, the design concept focused on an underground structure providing shelter from the harsh diathesis of the Martian environment, including extreme temperatures, radiation levels, weather, etc. Within this original concept, all units were interconnected through central common spaces, with sunlight channeled via sun shafts protruding above the surface
The concept later evolved into a habitat integrated within Martian canyons, leveraging the natural formations, such as those found in the Valles Marineris, to enhance construction feasibility and accessibility
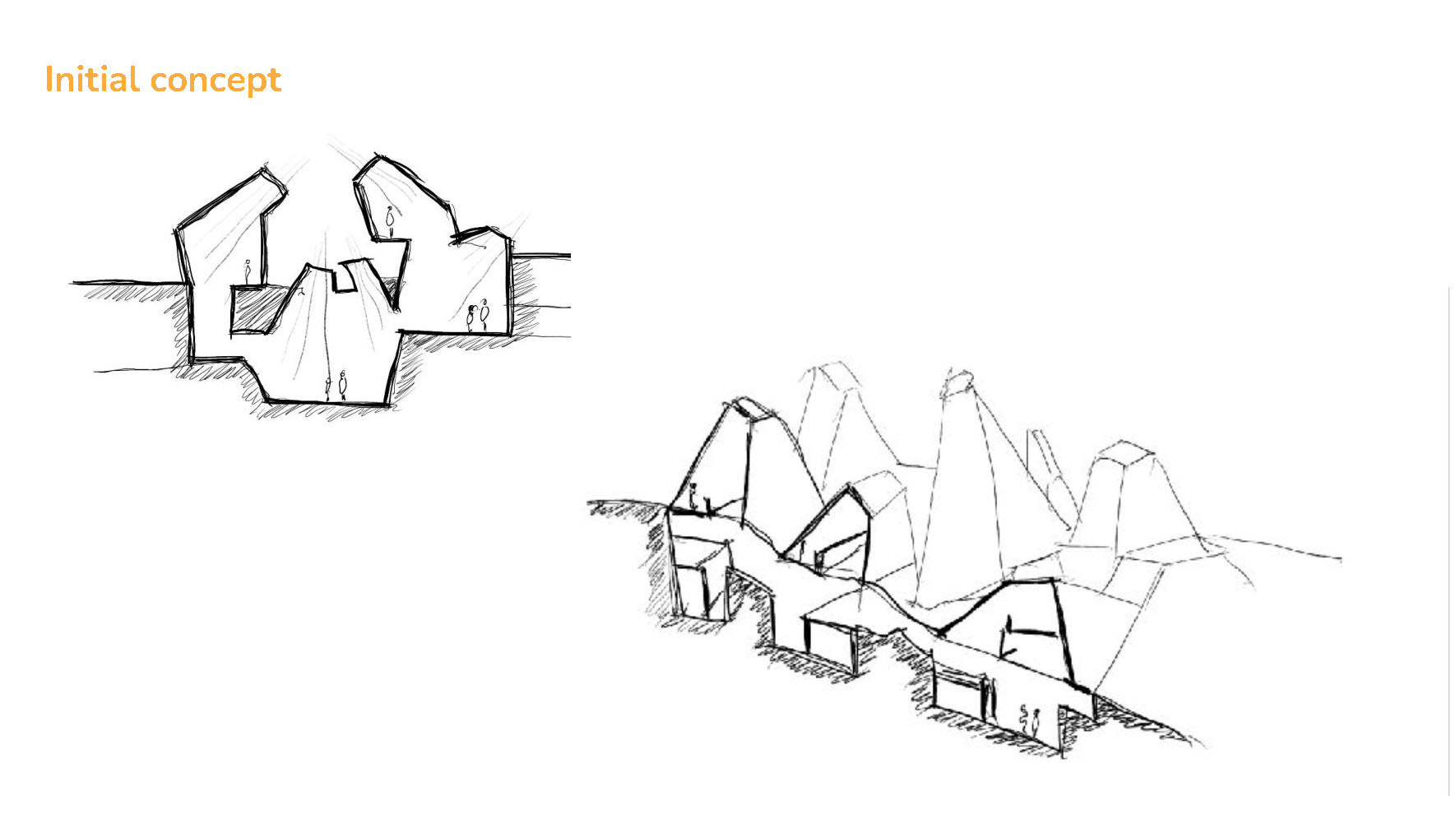
Sketches by group member
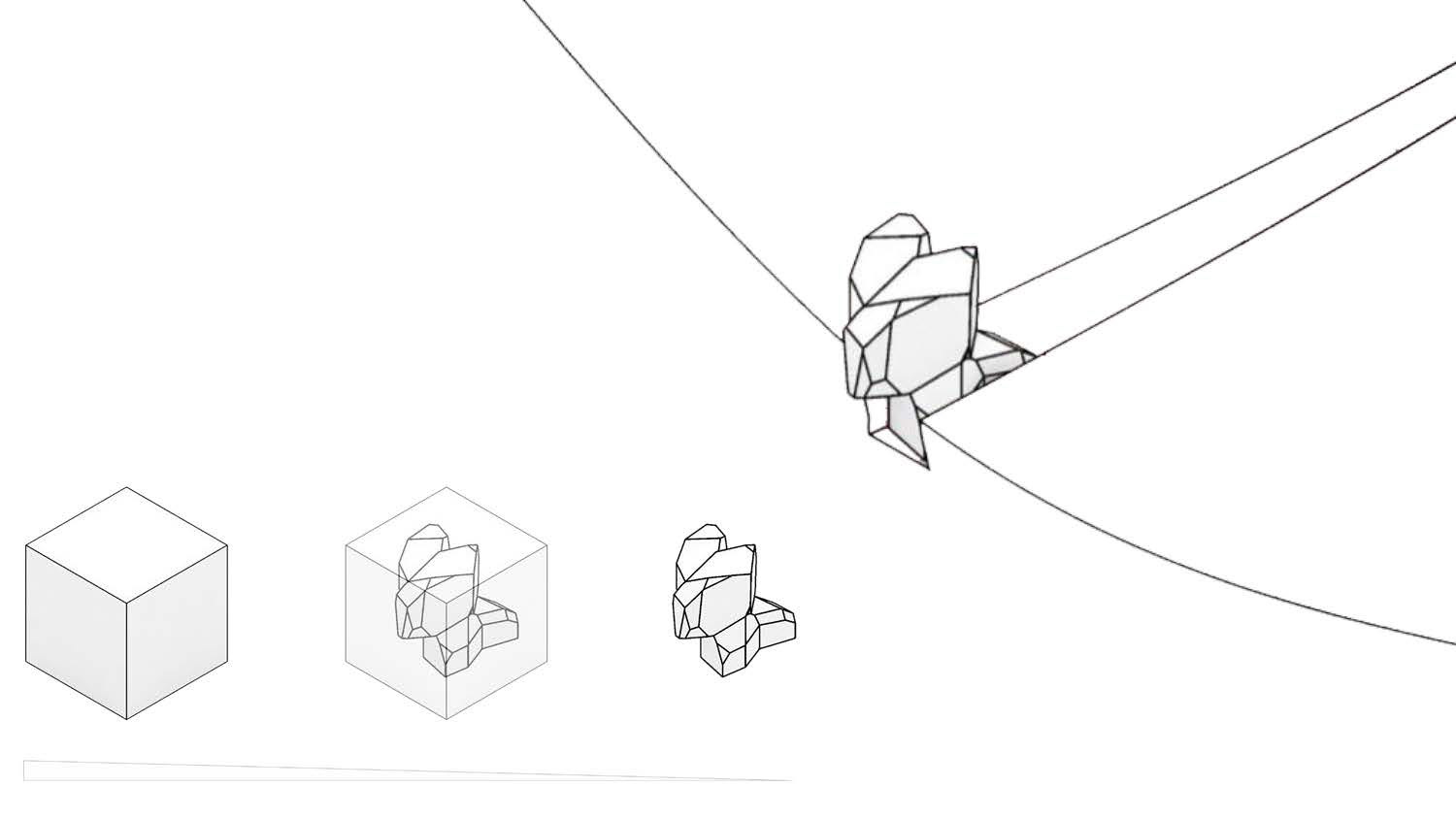
Design Development
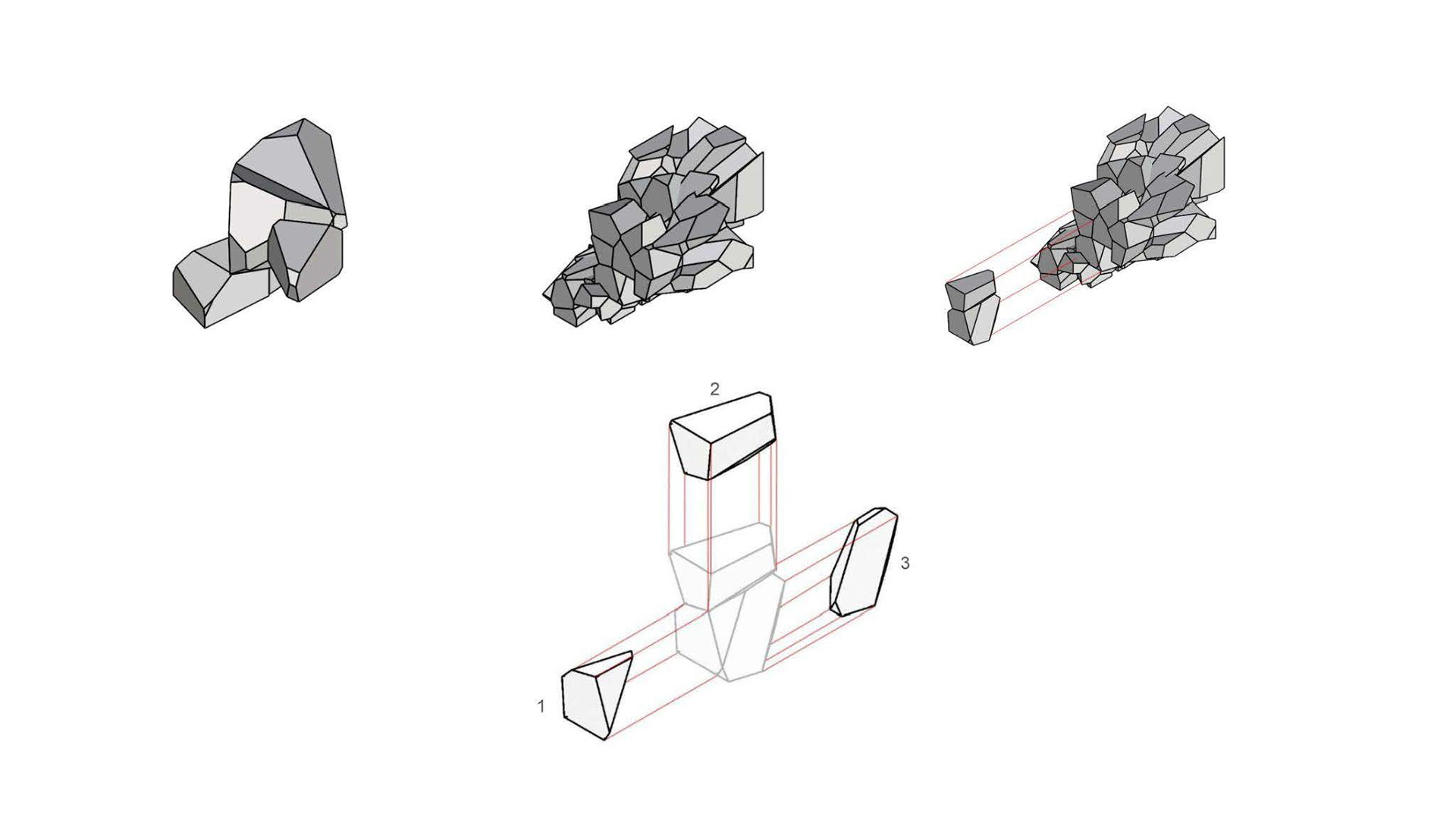
Splitting Voronoi
The habitat is anchored by a substructure designed to house essential facilities, with additional spaces allocated for expansion. For structural stability, the framework is securely embedded within the existing terrain. The external skeleton structure is integrated within the habitable spaces, ensuring on-site 3D printing and assembly feasibility without direct human interaction
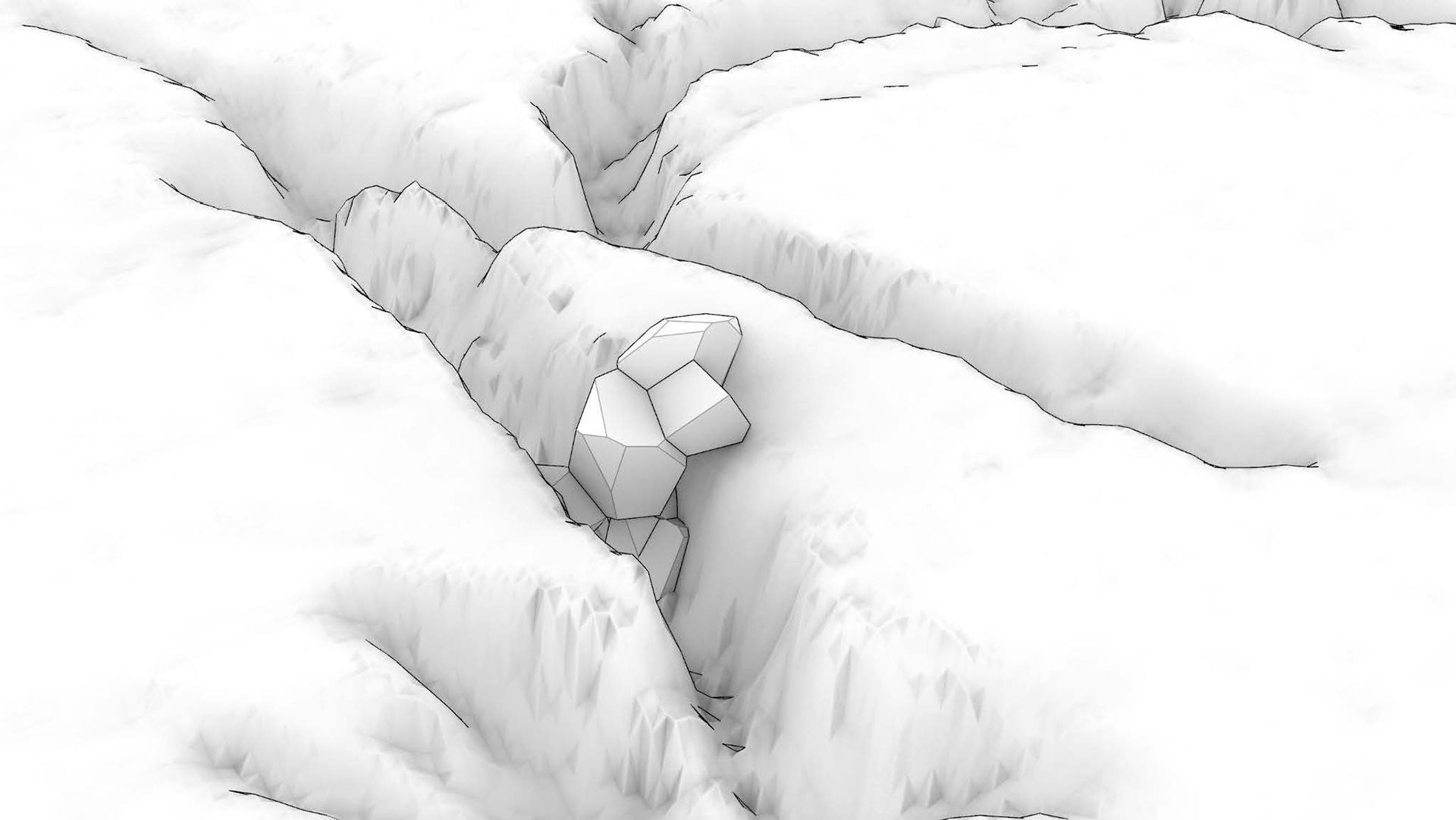
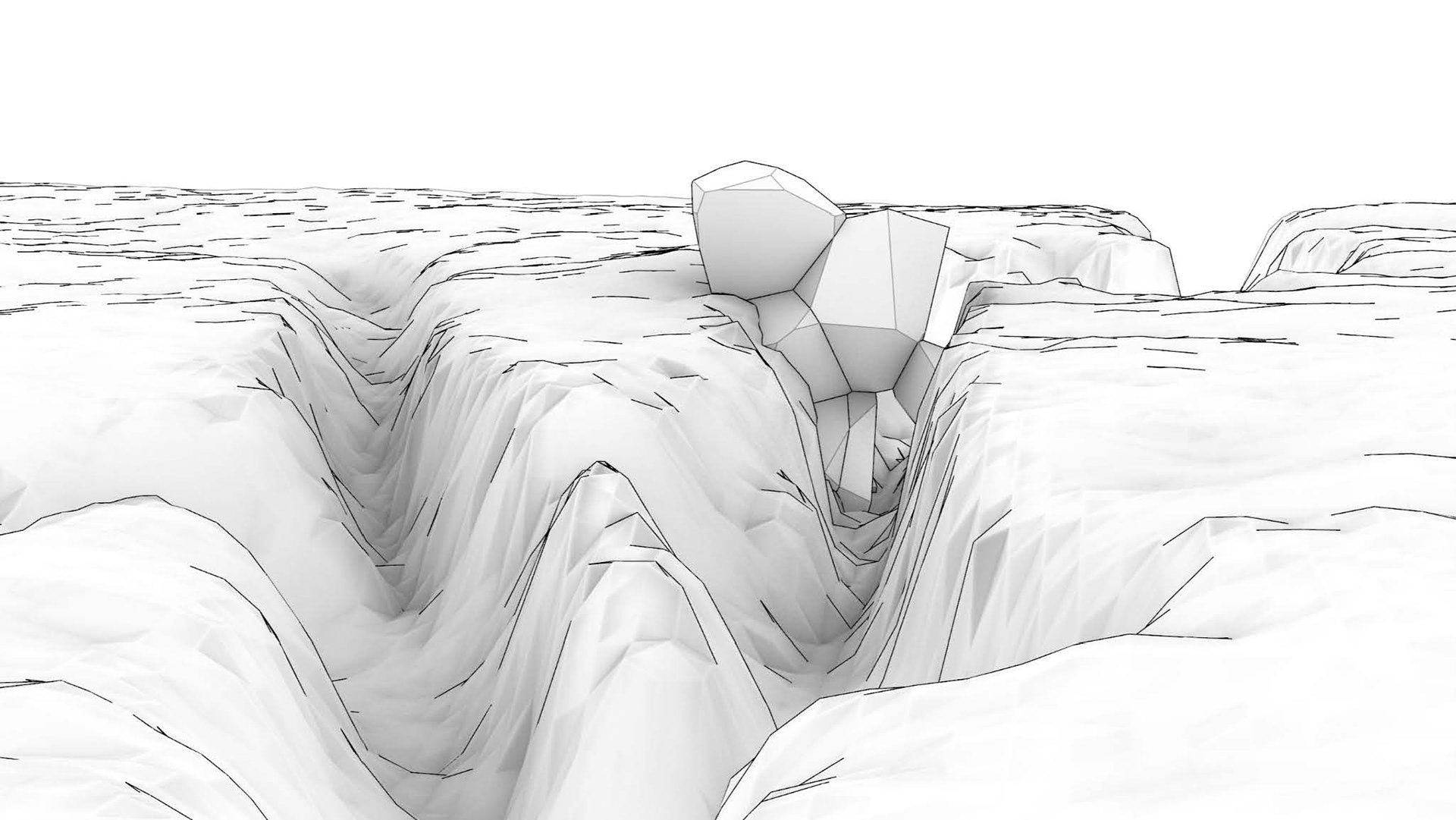
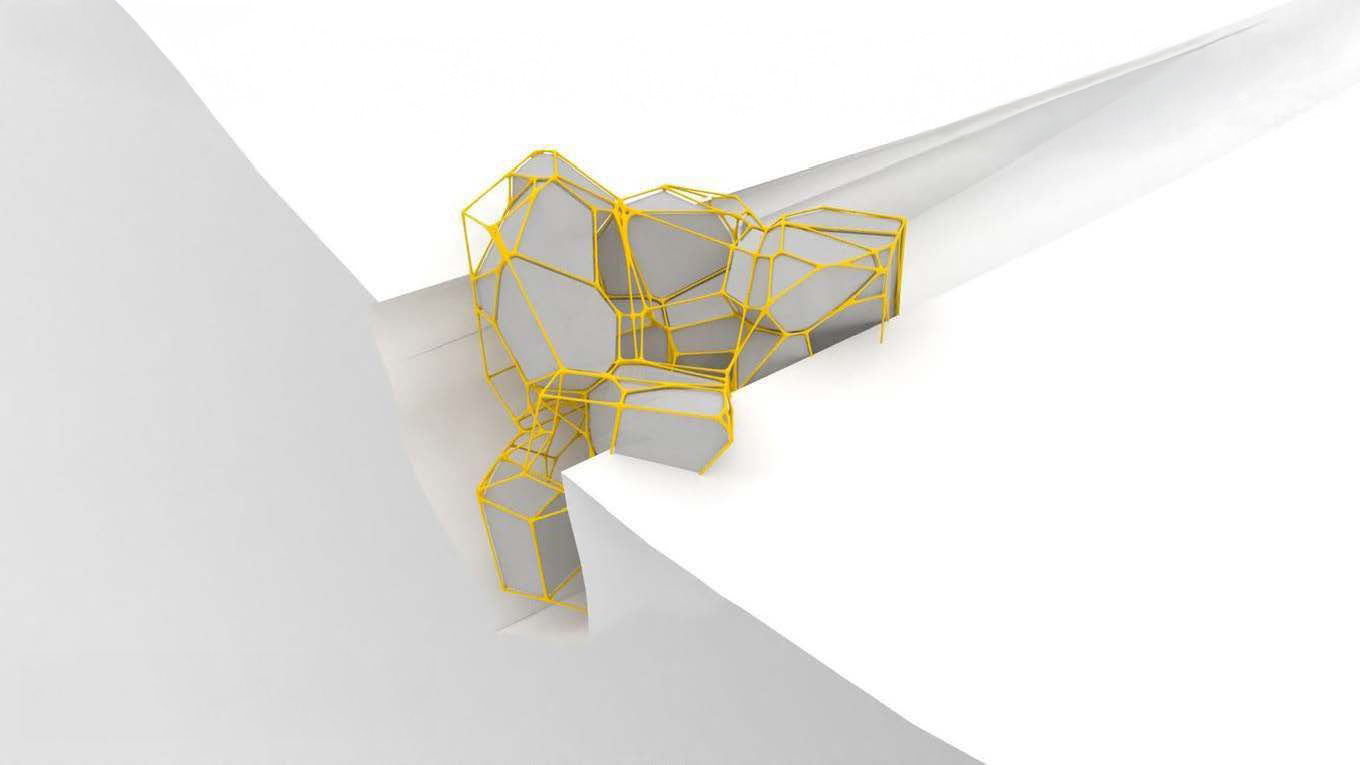
Structural Development
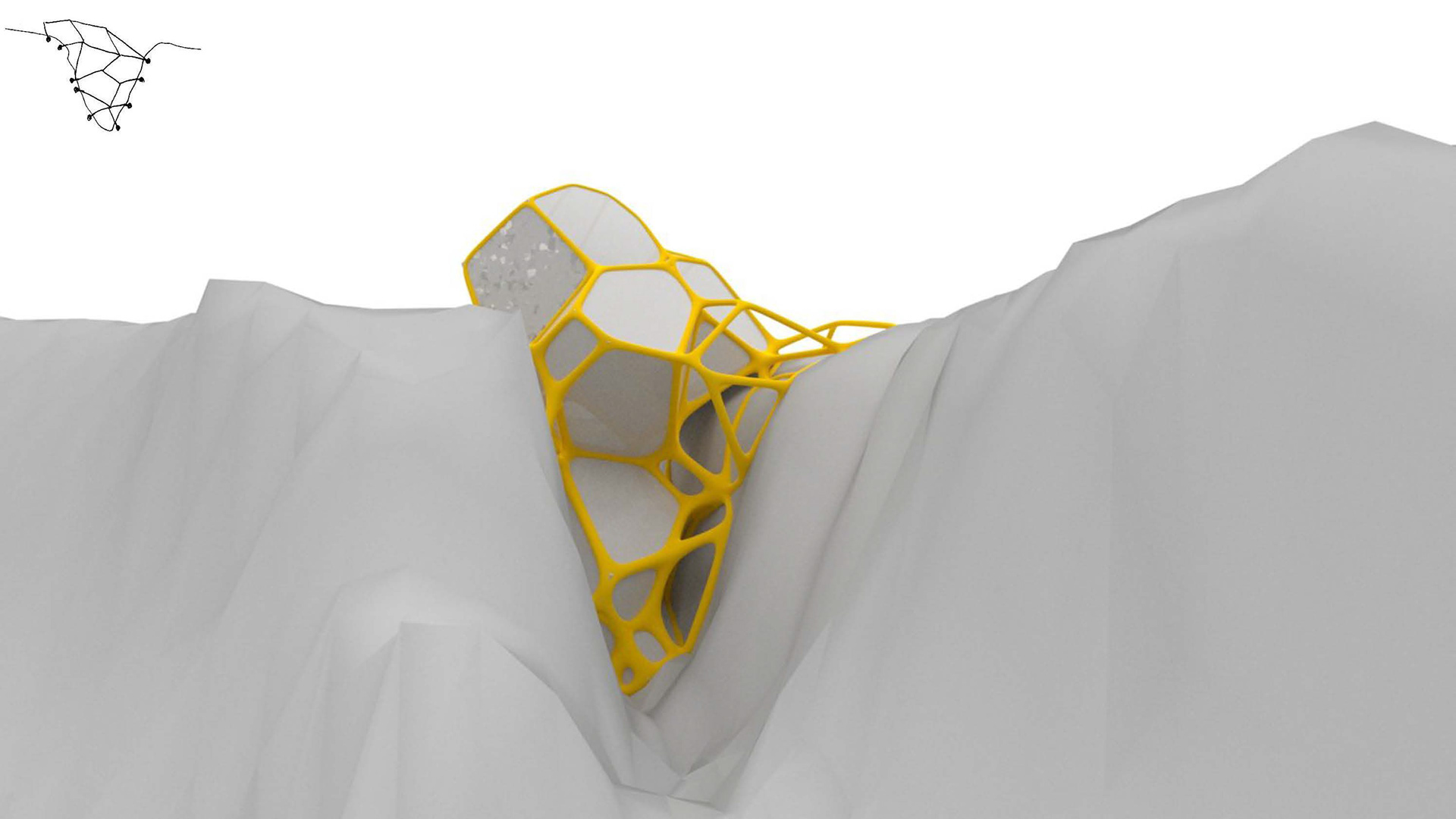
Structure Conformed to Valley
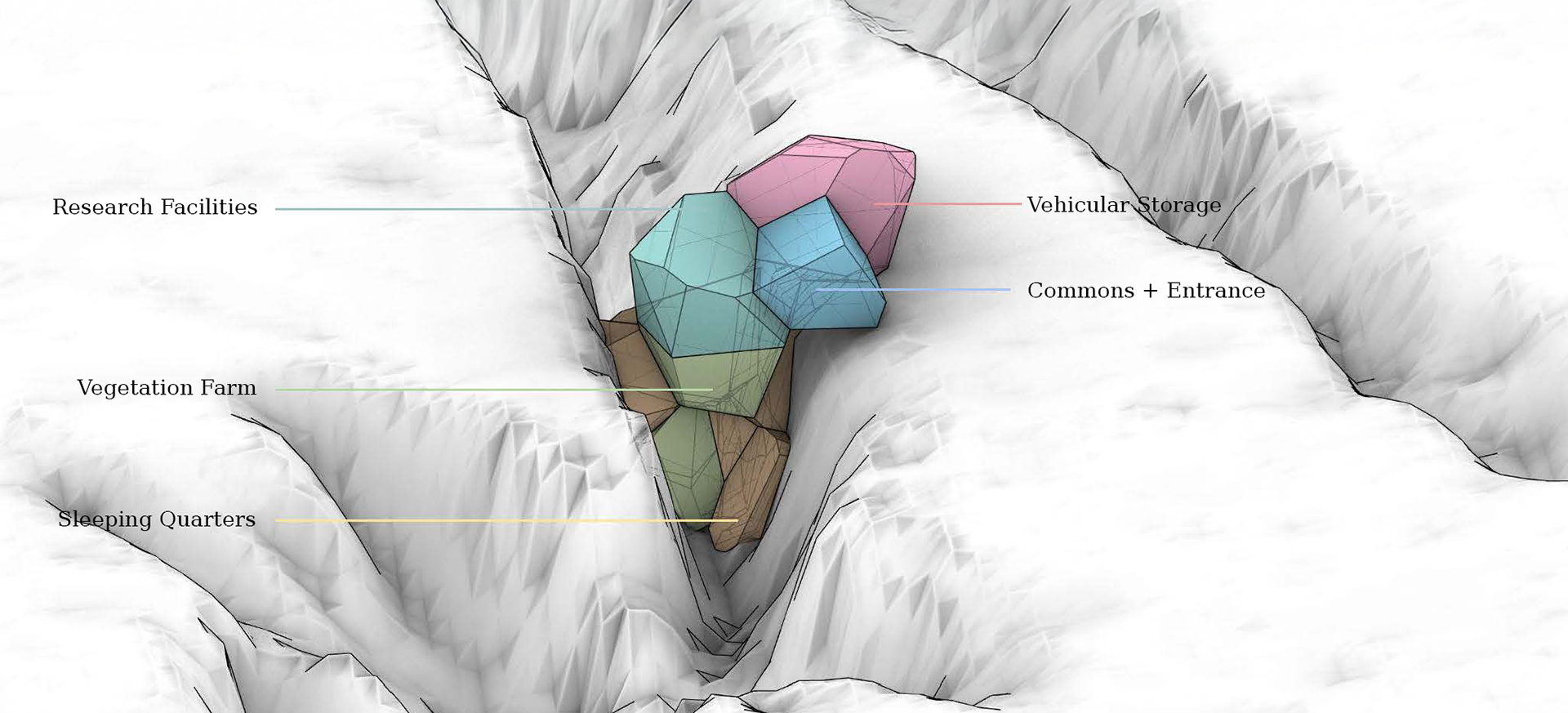
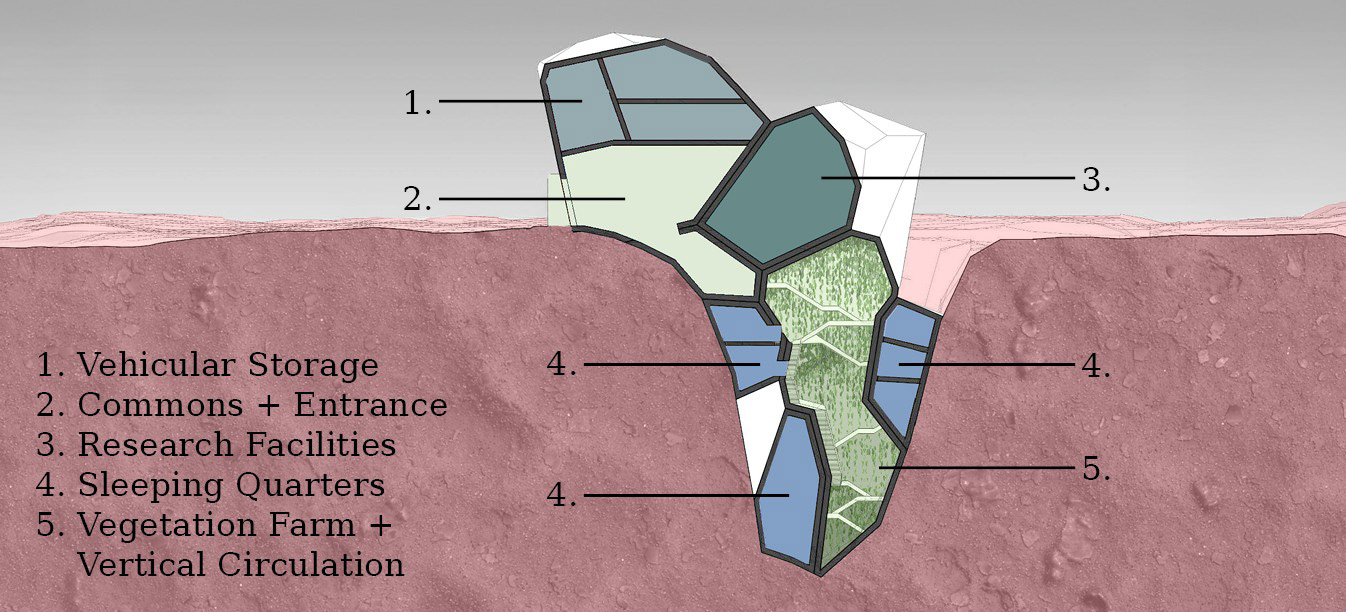
The following are the assemblable fragments carved out using a robotic arm as part of our proof of concept. Grab holes were strategically placed based on the specific assembly sequence and the operational constraints of the rover. These fragments were generated using Grasshopper to ensure precision and feasibility for on-site construction
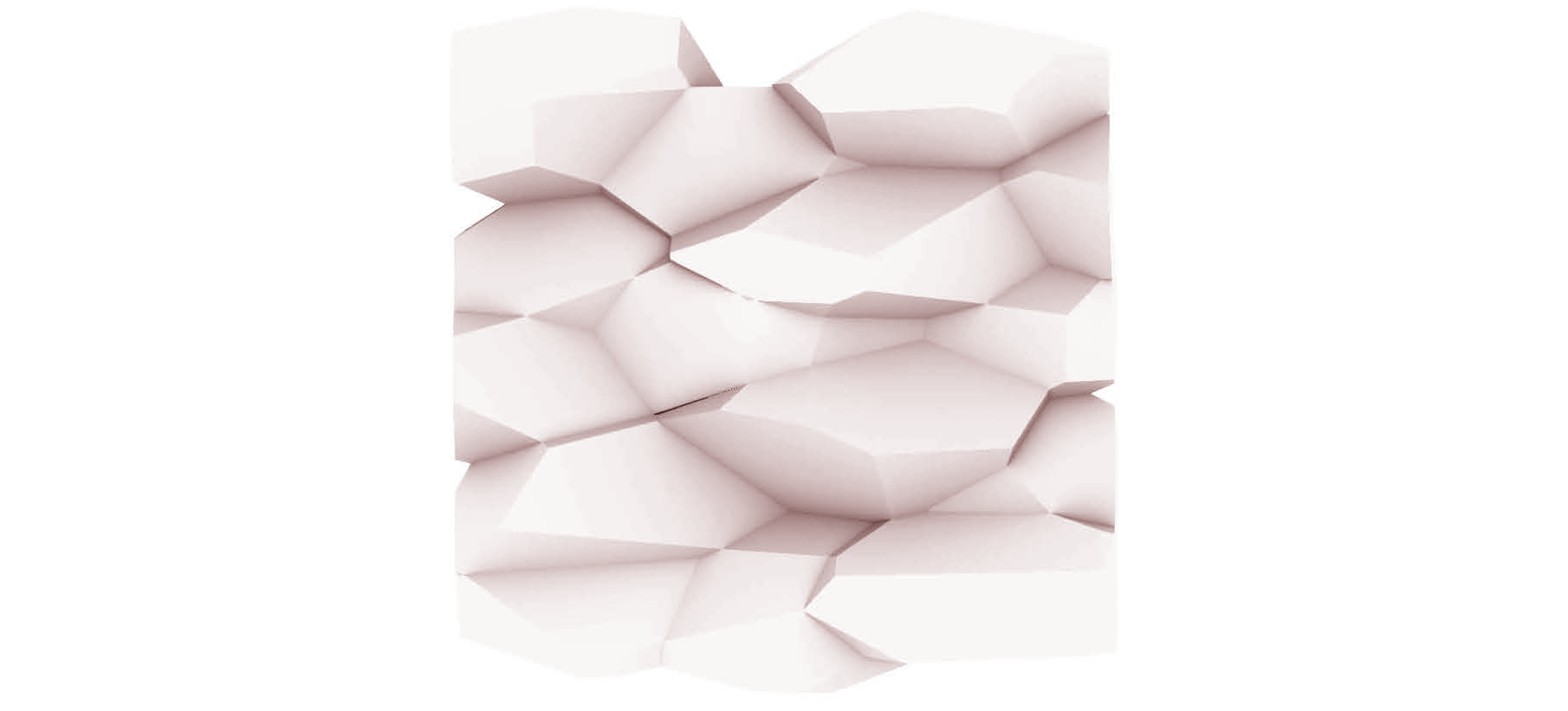
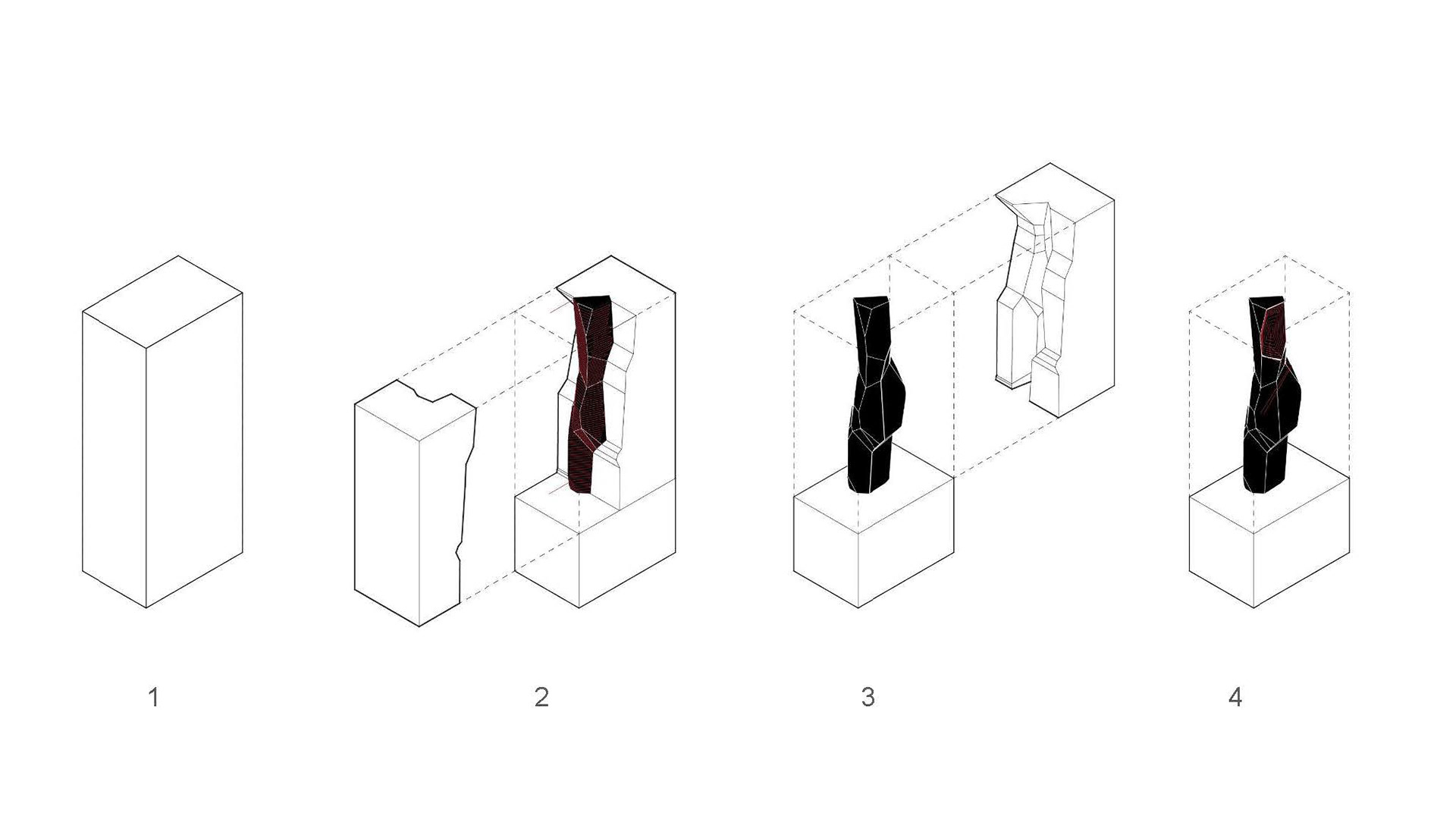
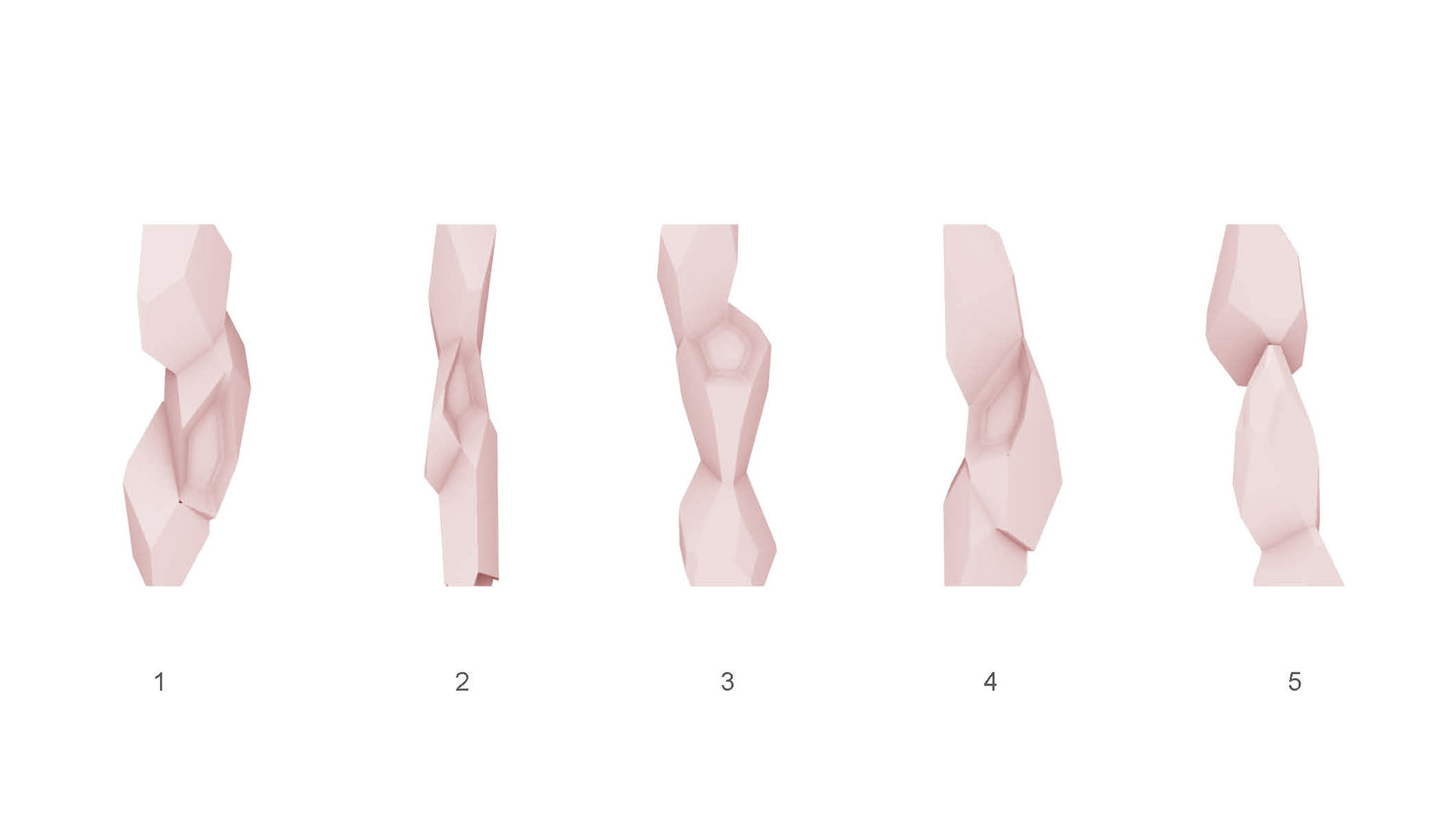
The robotic arm, programmed using Grasshopper, executed the carving process as demonstrated below. The process begins with a block of Styrofoam, as simulated in the first image. The fragment is split into two halves to accommodate the robotic arm's reach limitations and minimize potential disruptions during carving. The robotic arm carves laterally across the long side of the Styrofoam block, starting from the top and gradually moving downward, line by line. Once one side is fully carved, the fragment is rotated 180 degrees to allow the process to continue on the opposite side
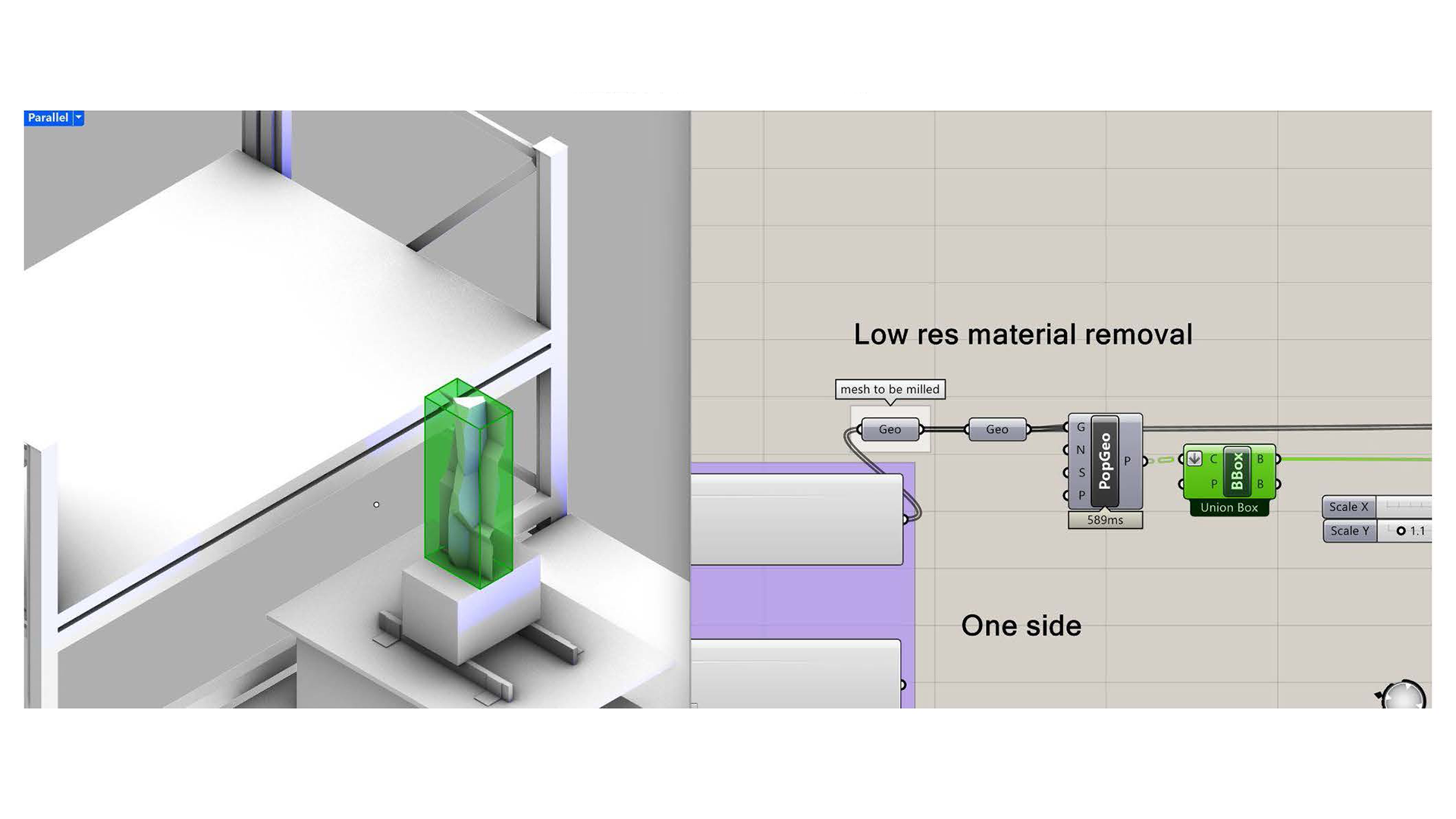
Simulating the starting shape of the styrofoam
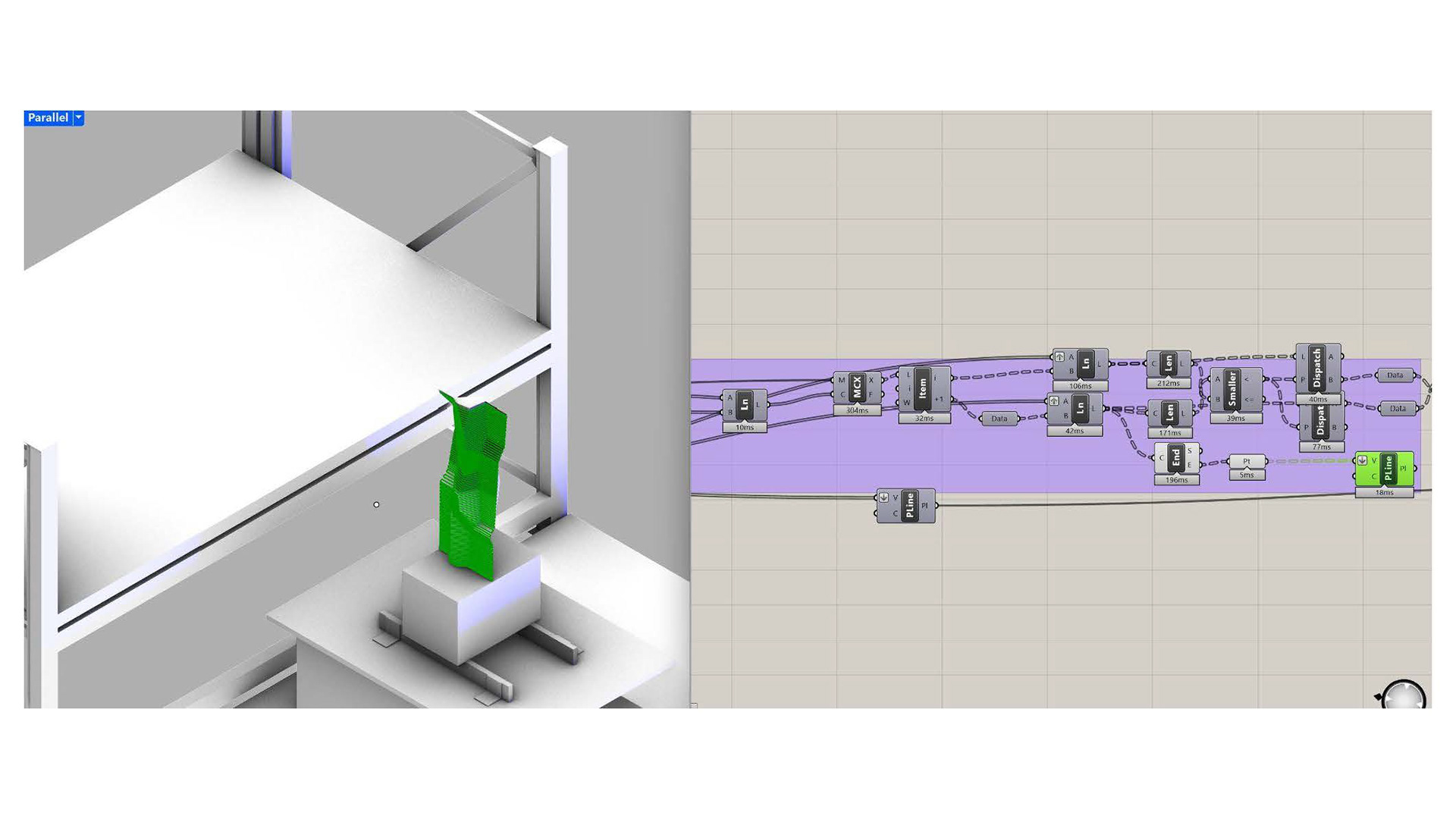
Determining the carving path of the overall fragment shape
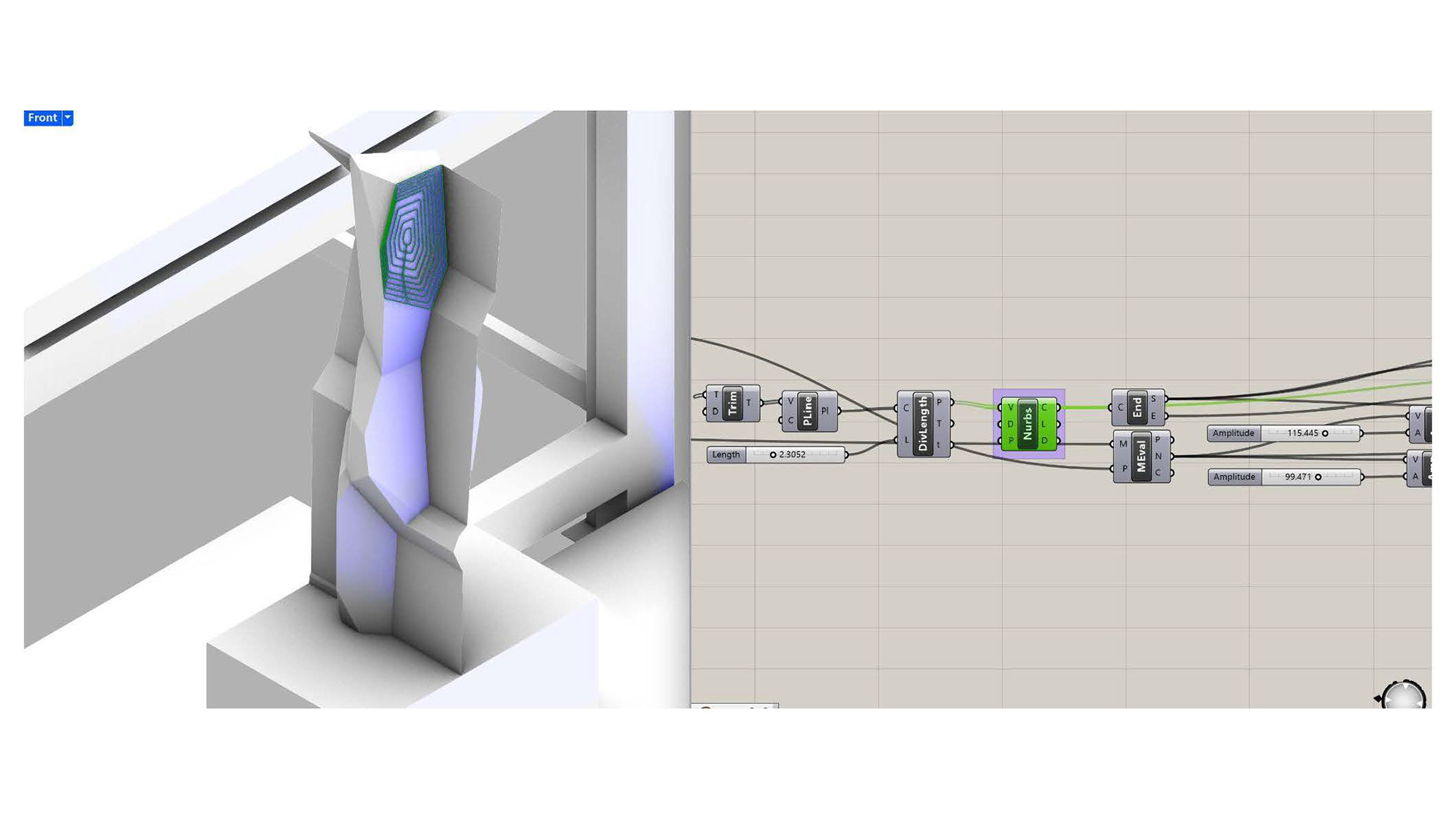
Determining the location of grab holes